Monday: Bathtub, faucets for vanity sinks and toilet installed. No water for the morning.
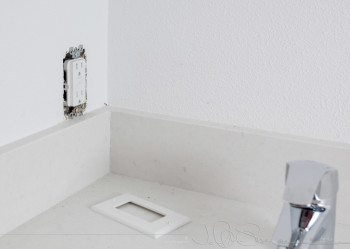
I asked Greg why the electrician didn’t put the outlet cover on – it won’t fit. It may have to be moved if cutting a hair off the bottom doesn’t do it. Funny thing is that I’d asked the electrician to make sure the socket wasn’t right against the wall – lots of evil appliances have huge plugs and I’d just had a case of something not fitting in the master bath because the socket was right up against the wall – they put the boxes on the studs. He did that part just fine…
Tub isn’t fully operational as it doesn’t have a stopper or overflow drain yet. Shower is coming “soon”. There was some discussion about a new 45 degree elbow for the handheld shower in the tub to deal with drips after use from the water remaining in the shower head. That sounds mad, so I’ve written to Grohe support to ask.
Greg was here at 7:30 to meet the plumbers (who weren’t coming until later) and at the end to clean out wood and debris from Jeffrey’s garage. Tomorrow we get some finish work on the garage construction…
Tuesday: Minor grout work on hall bath (shower niche, toilet paper holder and “rubber ducky” niches under tub). The shower itself was a victim of some ordering eff up, but will be here.
Vanity doors and drawers installed. The far drawer hits the anti-scald valve under the sink (it’s now required to mix cold with hot to 120 degrees maximum) which is why it sticks out. It needs a small notch cut in the rear of the drawer. The door and drawer edge pulls are another “soon” item, but they’ll look like this (but chrome).
The garage is getting back to “normal” – today it got some drywall over the new construction. This isn’t just about making it pretty – drywall is fire rated and it’s required by code to cover any wood in an area with any electrical.
Wednesday: Framing around the turned stairs – we’re now mostly closed off from the outside air! There’s a new location for one of the bonus room heating vents. Garage side now has drywall everywhere – next step taping.
Thursday: Site meeting with a very useful detour to the bonus room to review technical challenges to various plans for using the under eaves area for more shelves and storage. Everything can be done, but some things are too expensive to make sense – cutting into the knee wall studs to create built-ins requires re-framing for roof support as these are load bearing, not just drywall support.
Greg measured things and did minor fix-ups to drywall and cutting down a socket cover.
Friday: Walk through and measuring with the cabinet maker and stair company (for the bannisters for the back stairs). Lots of discussions about more details than I had imagined (for example: match existing crown molding or have simpler new type – how many inches? – to go with shaker cabinets). This took nearly 3 hours.
Also learned that code has changed since the house was built and our back stairs have too large a nose! The nose (where the tread sticks out over the riser) must not project more than 1.25″ and ours project 1.5″. An easy fix as the stairs are carpeted. The handrail down at the bottom also doesn’t meet code as it’s not high enough by about 2″ – the stair guy says we should replace that with rail and balusters at the correct height (if that’s too expensive we can build up the existing cap).
Plumbers came back to install the shower head, and the electrician installed the heated towel bar and turned the heated floor on. That floor feels soooo nice on bare feet! And look how spiffy the bathroom is today! We have to wait for the glass wall and door to be installed before we can use the shower though…