August 31 – whenever we get our house back
Is it obvious I’m really ready for this phase of the work to be done?
Putting the house back together is the next phase, but first there’s all sorts of touch up and finishing steps. We are all done with the all day/every day part at this point.
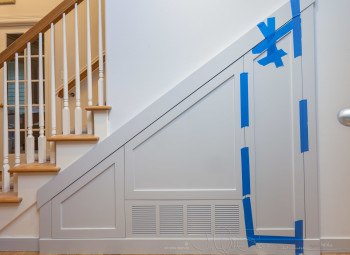
Week ending September 4th
Monday: Under stair cabinets. Painting in master bathroom skylight. Touch up paint. Cleaning up drywall overspray.
Tuesday: The installation of the Zephyr Milano vent hood has been a big pain – and that’s surprising as it’s a product that’s been out for a while and there’s nothing out of the ordinary about our installation – if you don’t count the slightly uneven ceiling. We already had the top of the duct cover cut to fit by a local metal working shop, but the stainless piece doesn’t fit around by about 1/2″
As I purchased the vent hood (at Westhill’s direction), I had to contact Zephyr product support. Strangely, over the phone you get to voice mail every time (we’re busy assisting other customers) but via e-mail (I sent them some pictures) they responded faster. After several back and forths – do they read what you write? – they had a suggestion and talked with Greg.
Stupid p*ssing contest with the electrical subcontractor about fixing things they didn’t do correctly . Losing a customer (we used them before the remodeling) over insisting every correction has to be billed as extra work, claiming things weren’t in the plans when they were and so on. However, the speaker wires in the bonus room are moved to the locations (roughly) shown on the plan. Now Greg will have to replace the trim at the bottom of the right hand slip in bookcases – they needed access to the eaves area.
Shelf holes in tall under stair cabinets don’t line up – shelves tip. Not entirely happy about how the front panel fits – seems to protrude a little. Greg pointed out a simple trick for slightly mis-aligned shelf peg holes: turn one of the pegs over (rounded side up). That’s enough extra height to compensate for the wobble.
Plan is for glass in the hall bathroom to be removed next Tuesday when the glass company comes to install the shower glass in the master bathroom. The tile company is coming to look at the problem with the floor heat next Wednesday if they can coordinate with the rep from Cosy Floor to be out here that day.
There will be an electrical final inspection and the electrician says we need new circuit breakers on all circuits except garages and bathrooms that have new sockets. Arc fault circuit interrupters are now apparently code in King County.
Wednesday: Painting the vent cover in the master bathroom and access panel cover in the downstairs hall ceiling (where the moisture sensor will go).
Adding insulation behind the bonus room bookcases (it had been removed eons ago when this project started). Replacing the trim under the bookcase slipins in the bonus room and painting touch-up.
The cabinet pulls for the under stair pullouts arrived and were installed. A neat trick for leveling slightly uneven shelves? Turn the metal peg that supports the low area upside down – it’s curved on the bottom and that fraction of an inch eliminates the wobble.
Thursday: Remove the family room doors and drawer fronts to return to KCN cabinets. They’re making new ones but want the doors to match sizes. KCN will be painting these with lacquer as the latext paint problems have not resolved and Westhill doesn’t want to wait any longer to see if the paint ever cures. The patch that the painters sanded and repainted (as a test) August 25th scrapes off, as does the back of the door paint from June 25th – that’s been curing for 10 weeks…
New screens from Milgard. They kind of fit – and aren’t damaged – but there’s a gap and they easily push/fall out. They’re in place for now, but I really think we need them to deliver a screen that fits – or hire Screenman to make two…
The screw heads came off on the back of one of the under stair cabinet pulls, but it’s not a custom size, so getting a replacement is easy and should be done tomorrow, along with the two wall TV mounts.
Week ending September 11th: We have the duct cover for the kitchen vent hood and new doors (lacquered, not latex painted) for the family room drawers/cupboards.
Week ending September 18th: On Thursday, the electrician came to install the Arc Fault Circuit breakers and was here for five hours! Apparently you need one socket on each new circuit with an AFCI test/reset switch (just like the GFCI sockets) and he had to install those. Not clear, given that the code requiring these is a year old, why these sockets weren’t installed in the first place. The electrician pulled out furniture to get at the sockets he needed to work on, didn’t put things back, didn’t clean up his mess…and then the inspector who came Friday said the AFCI sockets weren’t in the right place. They need to be the first socket in that circuit and apparently weren’t. So I guess the electrician will be back…
After an insanely long wait – first because the glass company was very busy, then because the hinges were back ordered – we have shower doors in the master bathroom! We don’t have the kitchen backsplash yet (no date on when that will be ready).
After they installed the glass in the master bathroom, they removed the door and glass wall in the hall bathroom in preparation for the tile underneath being removed to repair the heated floor. The screws attaching the bottom channel to the tile were 1.5″ long! The tile is 3/8″ thick and the channel bottom barely 1/8″, leaving 1 inch of screw to damage the heating wires. And the original installers told Westhill that their screws went no deeper than the tile…
Week ending September 25th: Monday morning the tile company excavated the hall bathroom floor to look at where the heated floor wires had been damaged. Both of the 1.5″ screws the glass installers used hit the wire – given the odds and the thin wire, you have to work hard to do that! Look at the closeup of the damage. The problem has been with us for months (see the Friday entry here) – and the electrician was right about location.
The rep from Cosy Floor who was supposed to be here Monday morning was stuck in Portland with car troubles. Now we wait for him.
Lots of work unpacking boxes and putting furniture back…
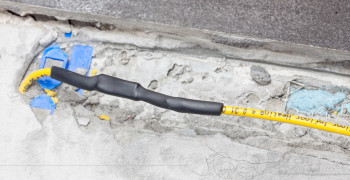
Tuesday at 1pm the Cosy Floor rep arrived. He had 13 years installation experience, even though he now does sales, so he was able to use the repair kit to fix the wire and the floor is now warm – yea! Inside the jacket, the wires are about the thickness of a hair and you need to join the correct ones (which you can’t tell apart if you just cut the wire to start a repair). So each strand was cut and spliced carefully.
The Cosy Floor guy said the way to move the wire over a little (to avoid it getting zapped again) is to unhook it from the blue plastic guide and tuck it around the adjacent one. He chiseled out enough mortar to free the wire from its holder.
Tomorrow morning the two excavated tiles will be replaced (was supposed to be this afternoon but they bailed) with the quick-drying thinset and midday the glass gets re-installed. We have to leave the glass for 24 hours before using the shower again.
I’m told that the kitchen backsplash will get installed on Wednesday as well. Greg (Westhill) mentioned it was odd that the tile company (who laid the floor) didn’t want to have someone on site to watch the Cosy Floor rep make the repair – seemed like a missed opportunity.
Wednesday, the tile was replaced and the glass wall & door re-installed. It needs to stay dry for three days for the tile grout to fully cure. The backsplash for the kitchen wasn’t the right size, so did not get installed. Unknown how long we’ll wait for a replacement (apparently you can’t cut tempered glass). The glass company does the measurements, but the guess was that they measured from the edge of the glass canopy down to the Caesarstone backsplash instead of from the center metal screen down. It’s slightly below the height of the glass.
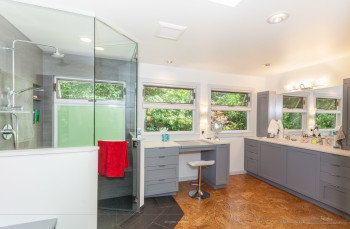
Sunday (September 27th) is the first day we’ve had two working showers in the house since March 16th!!
From March 16th through May 9th, we all used the old master bathroom while the hall bathroom was being demolished and put back together. The new kids bathroom with wet room is really great, but it wasn’t an en suite bathroom, plus all four of us sharing it wasn’t always straightforward.
On September 18th, we got shower doors/walls in the master and all four of us used the master bathroom again until the heated floor repair was finished in the kids’ bathroom. That was done on Wednesday but the grout on the tile had to cure for three days before getting wet, so today was the day both showers were back in service.
It has been a lovely sunny day and the light and views through the window and skylight are as lovely as I’d hoped they would be.
Week ending October 2nd: Monday, the electrician corrected the arc fault circuit that was located incorrectly (by using a new breaker switch instead of doing it on an outlet) and said he’d call for inspection Tuesday. No inspector showed! I asked the project manager to have it rearranged for Friday, but the electrician didn’t do that either…
Final inspection Friday. on the structural work to turn the stairs up to the bonus room . The cabinet maker came to look at one pair of doors that didn’t fit properly. He adjusted one side, but took the other door away to fix it.
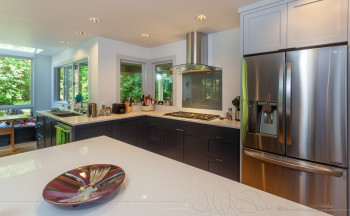
Week ending October 9th: We (finally) got the backsplash behind the cooktop Monday morning.
Week ending October 16th: We got two screens that fit for the kitchen windows! The Lake Washington Window and Door sales rep delivered them himself (I guess he didn’t want another set damaged in shipping…)